Chemical Resistance Guide
Harrington Online Chemical Compatibility Guide for Piping Systems
Harrington is a single resource of non-metallic and high-purity steel piping products. The chemicals listed are classed alphabetically according to their most common designation. Further descriptions include trivial/common names and some common names.
Guide Legend and Use
Temperature (°F) = recommended for use at or below this temperature (results shown in green)
X = Unsuitable, do not use (results shown in red)
C= Caution, actual testing necessary (see note displayed for detail) (results shown in yellow)
- = Insufficient data, testing under actual use conditions required
* = See Note displayed for further explanation
Seals (Carbon & Ceramic)
A = Acceptable (results shown in green)
NR = Not Recommended (results shown in red)
– = No Data, testing under actual use conditions required
High Purity Metallic Tubing
A = Excellent (results shown in green)
B = Good, minor effect (results shown in lighter shade green)
C = Fair, needs further testing under actual conditions (results shown in yellow)
X = Not Recommended (results shown in red)
- = Insufficient data, testing under actual use conditions required
NOTE: an A-rating for metals indicates that the rate of penetration is < 2 mils per year; a B-rating indicates rate of penetration < 20 mils per year; a C-rating indicates rate of penetration <50 mils per year.
- Locate the specific chemical in the guide.
- Select the material with a maximum use temperature that matches or exceeds the need. The Harrington philosophy has always been to suggest the least costly material that will do the job.
- Where a material or elastomer appears to be marginal compared to the requirements, place a call to our HarringtonTechnical staff for additional recommendations.
- Methylene chloride: in the table PVDF, Halar, or PTFE are the only materials suitable. Carbon steel works well for chlorinated hydrocarbons of this sort, and that would be our choice unless there was another reason to justify the higher cost of PVDF, PTFE, or Halar.
- Sodium hypochlorite, 15% at 100°F: PVC is good to 100°F and is the least expensive of the materials available, however, you must use 724 CPVC cement for this and caustic applications.
- For nitric acid, 40% at ambient temperature: the tables recommend either CPVC or polypropylene at 73°F. In most cases, CPVC will be the economical choice. Note that PVDF is rated for higher temperature use.
Apple iOS App & Google Android App
Harrington is proud of our new Chemical Guide for Piping Systems, available for download on the Apple App Store and Google Play Store. The Harrington Chemical Guide is a reliable tool that can be used in conjunction with other resources to help determine the most appropriate piping material for a given chemical.
The Harrington Chemical Guide for Piping Systems is available for free on Google Play and the Apple App Store for iPhone and Android Phones.
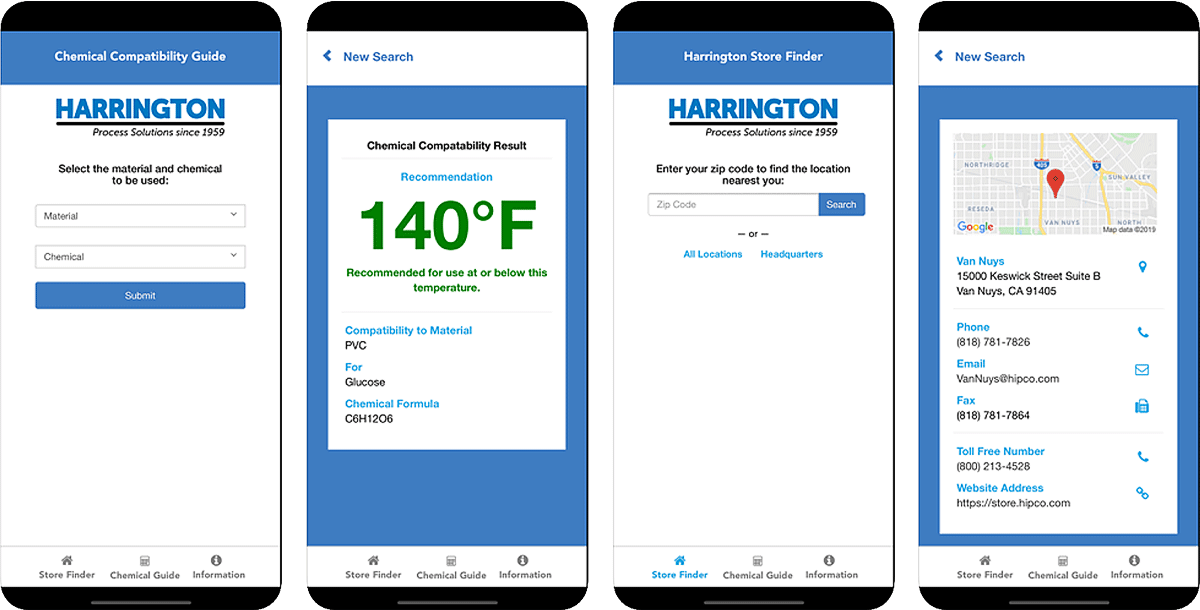
The Harrington Chemical Guide includes data for 23 different types of plastic piping materials, elastomers, pump seals, and high purity metal tubing and compares them to over 880 different chemicals. This comprehensive data can be used by the engineering & end-user communities as a guide toward helping make informed decisions on chemical compatibility of various piping materials for their specific process or application. In addition to chemical compatibility, the app also has a Store Finder, Company Information, and links to Harrington’s e-Commerce website.
The following information is provided as a general guide for the selection of piping systems subjected to various chemical substances. The recommendations stated are based on information provided by our manufacturers, raw material suppliers, and our extensive field experience, and is believed to be reliable. This information is based on one or more of the following: actual chemical immersion testing, chemical structure comparison to substances that have been tested, past field experience, and various other sources.
Numerous variables and environmental factors such as percentage of chemical concentration, combinations of chemical substances, temperature, internal pressure, exposure to the elements, external mechanical stress, and product quality can affect chemical resistance of plastic piping systems when exposed to chemical media. Although extensive research has been conducted over the years to better define use parameters, the possible combinations of chemical mixtures and their resultant reaction when mixed are endless. Therefore the following chemical resistance data is meant to be used as a general guide and is by no means complete. When test data on chemical resistance to particular chemicals under specific operating conditions is not available, Harrington Industrial Plastics LLC. recommends that chemical immersion testing be performed, and if successful, a small test assembly be constructed to test the product under actual use conditions (appropriate care and safety precautions must be followed with all in-service testing and product use).
In all cases, a physical test of the material under actual operating conditions is the only way to ensure the success of a particular material for the application.
Plastic piping continues to gain wide acceptance and use in many different industries and applications, particularly increased use in commercial plumbing applications. As a result of increased use in the commercial construction environment, plastic piping products are exposed more frequently to contact with ancillary products as well as exposure to other trades. Occasionally certain chemicals and ancillary products found in construction products and specific site preparations can cause damage to plastic piping systems.
Plastic piping products can be damaged by contact with chemicals found in some construction and ancillary products such as thread sealants, lubricants, anti-freeze solutions, fire stop materials, etc. It is important to verify the compatibility of materials that come in contact with the plastic system to ensure long-term performance.
Contact Harrington Technical Services or your local Harrington with questions regarding chemical compatibility.
The chemical resistance data in this guide has been obtained from numerous sources, and to the best of our knowledge, the information contained in this publication is accurate. However, Harrington Industrial Plastics, LLC does not assume any liability whatsoever for the accuracy or completeness of such information, and retains the right to revise this information at any time. As the conditions or methods used are beyond our control, we do not assume any responsibility and expressly disclaim any liability for any use of this material. To the extent that any hazards have been mentioned in this publication, we neither suggest nor guarantee that such hazards are the only ones that exist. Final determination of suitability of any information or product for the use contemplated by any user, the manner of that use, and whether there is any infringement of patents, is the sole responsibility of the user. We recommend that anyone intending to rely on any recommendation, or use of any equipment, processing technique, or material mentioned in this publication verify that all applicable safety and health standards are met. We strongly recommend the users seek and adhere to manufacturers’ or suppliers’ current instructions for handling each material they use. Compliance with all applicable federal, state and local laws and regulations remains the responsibility of the user. This information is offered in good faith and believed to be accurate at the time of its preparation, but is offered without any warranty, expressed or implied, including WARRANTIES OF MERCHANTABILITY AND FITNESS FOR A PARTICULAR PURPOSE.
In all cases, a physical test of the material under actual operating conditions is the only way to ensure the success of a particular material for the application.
- Compressed air or gas – Warning! Plastic Piping Systems designed for corrosive and/or high purity liquid service are not recommended for Compressed Air or Gas applications. There are a few specially designed thermoplastics piping systems that are suitable for selected Compress Air or Gas applications. Consult your local Harrington Office for recommendations. Certain substances called out on the following pages reference chemicals in a gaseous state. These substances are not recommended for pressure service. They are shown to provide the chemical resistance of piping materials when coming into contact with these substances. (i.e. exposure to or immersion in these substances). Harrington Industrial Plastics LLC, does not recommend the use of plastic piping systems for the testing, transporting or storing of compressed air or gases unless specifically designed by the manufacturer to do so.
- When investigating the chemical compatibility of a piping system, it is important to note that all piping system components must also be investigated for compatibility. Gaskets, o-rings, valve seats, pump seals, solvent cements, tanks, and other components and materials should be evaluated for compatibility and approved by their respective manufacturers for use with the fluid medium prior to use.
- The majority of the chemical resistance data provided in the following charts is based on chemical immersion testing run under non-pressurized conditions. Depending on the hazards of the chemical used, an additional safety and pressure de-rating factors are typically applied to the standard working pressure rating of the product (shown for water). Standard temperature de-rating factors must also be applied to pressure applications at elevated temperatures.
- Individual chemicals that do not have an effect on the pipe material may affect the pipe if combined with certain other chemicals – the information in this guide does not address combinations of chemicals.
- The suitability for use of a piping material in a particular process piping application is a function of: the specific pipe material itself, piping dimensions, construction, and quality, joining system, concentration of chemicals and chemical mixtures, operating temperatures (including temperature swings), operating pressure (including cyclical variations), applied stress, and life cycle information (i.e. material costs, installation costs, desired service life, maintenance, repair and replacement costs etc.). Users must make their own assessment of the suitability of the product for the purposes required.
- Chlorinated and aromatic hydrocarbons, esters, or ketones are not recommended for use with PVC or CPVC thermoplastic piping materials. Although the chemical resistance of PVC and CPVC compounds is similar, they are not always the same. Caution should be used when comparing the chemical resistance properties of PVC Type I, PVC Type 11, PVC Clear, and CPVC as differences in chemical resistance exist.
- Caution should be exercised when selecting thread paste compounds, lubricants, cleaning and wetting agents (surfactants), corrosion inhibitors and other chemical substances that come into contact with the system for compatibility as well.
- Applications involving certain oils, surfactants, and greases and certain other chemicals may result in environmental stress cracking. Environmental stress cracking occurs when the piping and components are weakened by contact with these chemicals, and failures are propagated by external stress (i.e. pressure, expansion/contraction, installation. etc.) on the system.
- Exposure of Clear PVC to certain chemicals can affect the clarity of the product over time. Clear PVC maintains its physical properties when exposed to many substances, however, exposure to sunlight (UV) and certain nitrogen containing organics, bleaches, oxidative agents and acids will result in discoloration. Testing under actual use conditions is recommended.